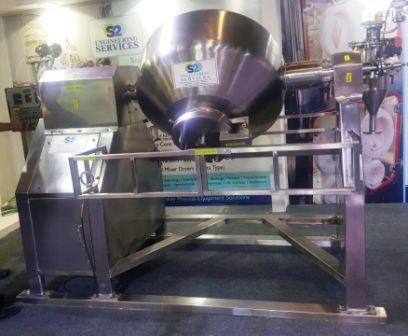
The first step in choosing a vacuum dryer is to determine what size batch you will process. Once you've established the batch size, consider which dryer type will drive up the temperature difference between your material and the heating media (ΔT) by controlling temperature and vacuum with an appropriate heating system and vacuum and solvent-recovery system. The greater the ΔT, the shorter your drying cycle will be.
Selecting components in the dryer's vacuum and solvent-recovery system requires considering your material's moisture content, because the ease and rate of vaporization in your application will depend on your material and the liquid in it. Key variables to consider are the amount of liquid in the material and the nature of that liquid.
Ask, "How much liquid must be removed? Is the moisture bound to the particles, in pores or capillaries or through molecular absorption? Or is it unbound moisture that will vaporize quickly?" Be aware that different liquids have different vapor pressure profiles at different temperatures.
You need to specify a vacuum and solvent-recovery system that can handle peak loading, not just the average vaporization rate for your drying cycle. Engineering the right system with the right components will ensure the dryer achieves the temperature, pressure, and solvent-recovery capacity you need.
S2 Engineering will help in the selection of the dryer. S2 go through a dryer selection application questionnaire for the application. The information includes your material characteristics, characteristics of the liquid to be removed, and drying requirements. You'll also need to explain what resources, such as electric power, heating, and cooling are available at your plant; whether your process requires solvent recovery; and whether you need associated material handling equipment such as loading or conveying equipment.
For further information please contact the S2 Engineering Technical Team.